Recycling – a sustainable solution for crushed slate
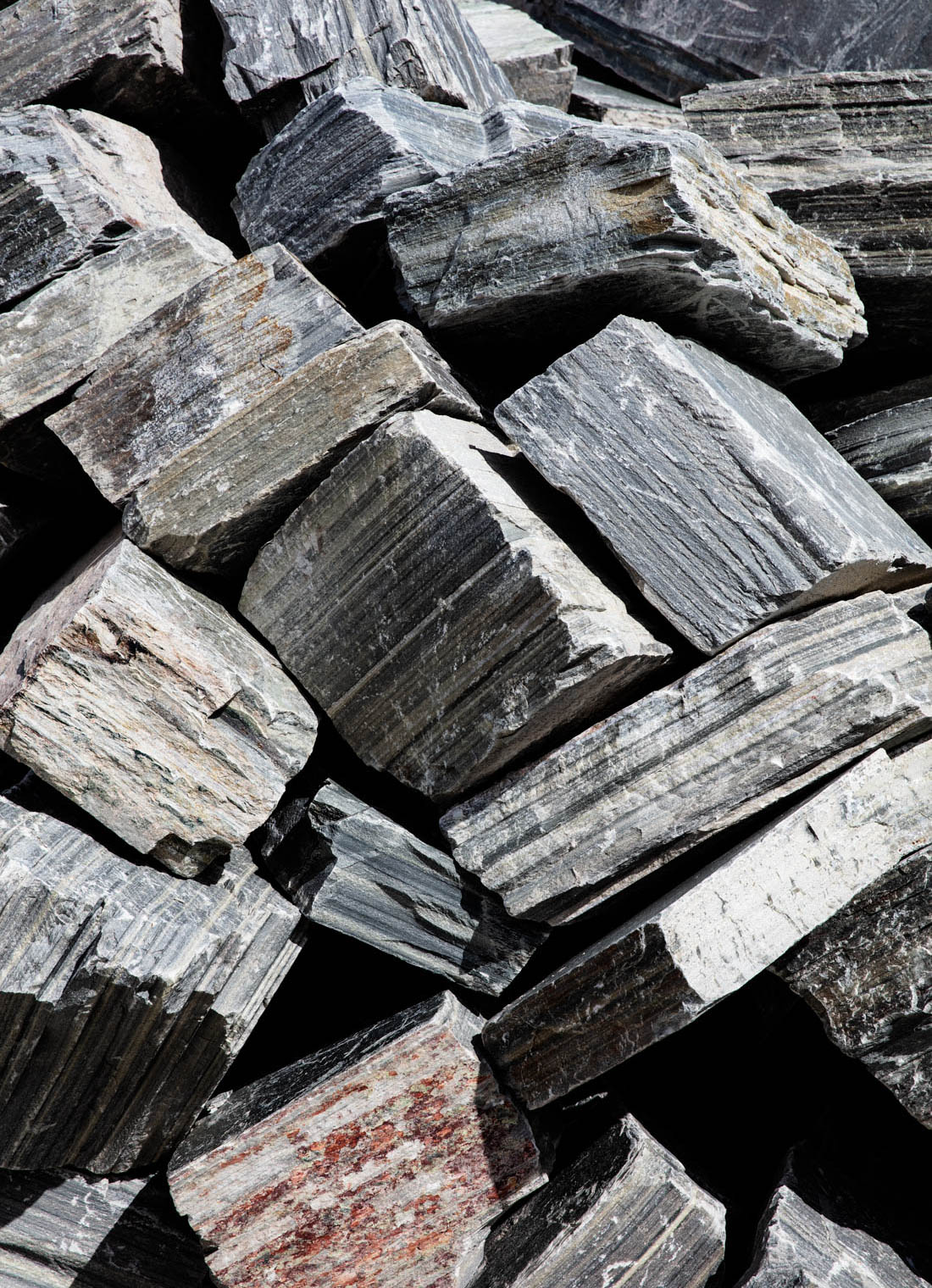
A research project led by SINTEF, an independent research organization in Norway, is showing how surplus slate material can benefit the environment and also generate a profit.
A research project led by SINTEF, an independent research organization in Norway, is showing how surplus slate material can benefit the environment and also generate a profit.
Every year, around 300,000 tonnes of slate are left over from slate quarrying in Oppdal, Norway. Could this surplus material be put to good use? This was a question that the slate companies in Oppdal and Forset Grus AS in Klæbu began to ask themselves, resulting in the Skifer Unik II project.
– Previously, it was assumed that, due to its special properties, slate could not be crushed and used for construction purposes. This was the myth we wanted to bust, says Lisbeth Alnæs, research manager at SINTEF. She has worked on the SkiferUnik II project, to be concluded this summer, since 2018.
Surplus slate has previously been dumped in land-intensive landfills. The surplus material, which represents a great expense for the business, can become a resource if the right application can be found.
It is estimated that the 300,000 tonnes of surplus slate matches the annual volume of crushed aggregate used by the region for road and construction purposes.
As Lisbeth Alnæs explains: – Road construction requires crushed aggregate of different sizes, in different layers.
So far, the results are positive.
– Down at the bottom, you usually need a frost-resistant layer below a reinforcement layer, and then a bearing layer. Crushed slate can be used in all these layers, she explains.
Crushed slate has already been used on a smaller scale, mainly in connection with land development, for ditches, as garden shingle and, not least, as grouting sand. The project is also investigating use of crushed slate in concrete.
– With concrete, properties other than strength also determine suitability, but slate fulfils the physical and chemical requirements, so the project is about to begin some test casting, she says.
She hopes the results will enable the collaborating parties to decide whether to establish a crushing facility for the production and sale of crushed quartzite slate from the quarries in Oppdal.
– I think it’s really great that the companies want to work together towards a common goal: to utilise the resource 100 per cent. Nowadays, many people are concerned about leaving as small a carbon footprint as possible and at SINTEF, we want to help with this, she concludes.
It was a natural step for Minera Skifer to become part of the project.
– First and foremost, it’s about resource management. We want to be able to use all the stone we quarry in the best possible way, explains Håvard Sæteren, production manager of the Oppdal department of Minera Skifer.
To make roof tiles of a sufficiently high quality for use on houses and cabins all over Norway, some poorer-quality slate always has to be removed first. Previously, this surplus slate would be deposited somewhere locally.
– Leaving as small a carbon footprint as possible has always been important for us. We’re incredibly pleased that we can now fully utilise something that was previously a waste product, Håvard Sæteren says.
He notes that it also has a green knock-on effect.
– If it leads where I hope it will, it may not be necessary to open quarries especially for this type of filler elsewhere in Norway. Hopefully, we’ll be able to meet the need for this material, at least in our region.
In the first instance, the idea is to use the surplus slate for gravel and crushed aggregate, and later on in concrete.
– We plan to have a commercial strategy for this during the course of the year, he concludes.
– I think it’s really great that the companies want to work together towards a common goal: to utilise the resource 100 per cent. Nowadays, many people are concerned about leaving as small a carbon footprint as possible and at SINTEF, we want to help with this.
Lisbeth Alnæs
Research Manager, SINTEF